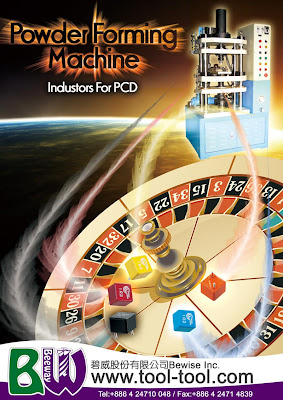
Bewise Inc. www.tool-tool.com Reference source from the internet.
The following article is a synopsis of an application note written by Bruce Carsten for Micrometals, Inc. followed by a section on PFC Design Guidelines written by Micrometals. The unabridged original version of the Bruce Carsten application note is available upon request.
The boost preregulator “front end” is increasingly used with AC line inputs to obtain an (essentially) Unity Power Factor, or UPF. Calculations of the core losses in the main inductor is problematic, however, as AC flux in changing continuously in a complex manner even with “fixed” input and output voltages.
The basic AC-DC boost preregulator power circuit is shown in Figure 1. The operation of this circuit is generally well known; the duty cycle of the main switch Q1 is controlled by logic (not shown) to boost the rectified line input voltage “Vi” to the output voltage “Vo”, while forcing the short term average input current (=L1 current) to be proportional to the instantaneous AC line voltage. Since the AC line voltage is (ideally) sinusoidal, the line current is also sinusoidal.

Figure 1
Basic Unity Power Factor boost preregulator power circuit
The actual control technique and circuit used are largely irrelevant to the calculation of losses in UPF boost preregulators. The loss calculation approach used here is generally applicable to constant switching frequency circuits where the boost inductor current is above “critical”, or continuous, throughout most of the AC line cycle.
A sinusoidal input voltage, constant output voltage and constant conversion frequency are assumed for calculating the (relative) AC core and HF winding current losses in the main inductor (L1). The peak HF AC flux in the inductor core can be calculated from the switching voltage waveform. A convenient formula for peak AC flux “ ˆB ” in CGS units is:

The maximum flux “ ˆB max” occurs when:
Vi =Vo/2
Where:
Vi = "Instantaneous" Input Voltage
Vo = DC Output Voltage
The actual switching frequency AC flux varies over the AC line voltage half cycle. Curves of ˆB / ˆB max vs. AC line phase angle q, for various ratios of Vi/Vo (where Vi = Peak AC Input Voltage) are plotted in figure 2

Figure 2
Relative Peak Flux in L1 Core vs. AC Input Voltage and Phase
At a constant switching frequency, the core loss “Pfe” will vary as ˆB n, where the loss exponent “n” is typically between 1.65 and 3 for most magnetic materials, including powder iron materials. The ratio of average core loss (over an AC line voltage cycle) to the “maximum” loss (at Vi = Vo/2), for core loss exponents of 2.0, 2.5 and 3.0 are plotted in Figure 3.

Figure 3
Ratio of Average to Maximum Core Loss vs. Vi/Vo and Loss Exponent “n”
It can be seen that the ratio of average/maximum core loss reaches a maxima when the peak AC line/DC output voltage ratio is near 0.61. The core loss ratio is not very sensitive to the core loss exponent, being somewhat less for higher loss exponents, with the largest average/maximum ratio only ranging from 0.672 for n = 3 to 0.725 for n = 2.
Since operation at the loss ratio maxima will occur in most UPF boost preregulators, a useful rule-of-thumb is that the “worst case” average core loss will be 70% of the loss calculated for Vi = Vo/2, where the Peak flux is:

Iron Powder PFC Design Guidelines Extra care must be taken when designing and specifying iron powder cores for PFC applications due to the AC content and complexity of the core loss calculations. Most present day applications for iron powder cores can have ambient temperatures up to 55Cº. Therefore, the increase in temperature rise due to losses must be kept to a minimum.
It is important for a PFC design to be evaluated under the worst case conditions which will be at maximum power and in most designs when the peak input voltage is either at its lowest level or when the peak input voltage is .61 times the boost or output voltage. The worst case winding losses will occur at the lowest input voltage since this is when the maximum current will flow, but the worst case core losses will occur when the peak input voltage is .61 times the peak output voltage.
It is important to recognize that a PFC design dominated by core loss is not acceptable without first completing a thorough design analysis. It is generally recommended that the loss distribution be no greater than a 50/50% split between core and copper loss. In fact, a 20/80% or 25/75% split between core to copper loss is preferred. It is also important to remember that it is much easier to remove heat from the copper winding than from the core.
PFC applications mean that higher Peak AC Flux density conditions are often present in the core than traditional output choke applications. If an inappropriate core material or undersized core is selected, the core will be subjected to excessive high frequency core loss resulting in a temperature rise that can possibly lead to thermal failure.
Many designs today utilize variable speed fans in order to cool and “quiet down” the power supply. Even at a reduced power load condition, the effective AC flux density and resulting core loss of the PFC inductor can remain fairly constant. Only the copper loss (I2R) has been reduced. Extreme care should be taken since a reduction in fan speed can result in a higher than expected temperature owing to the reduction of air flow.
The best way to determine the “hot spot” core temperature is to drill a small hole midway into the core and install a thermocouple wire. The soundness of the thermocouple connection to the core is critical for accurate results. Close attention should be paid to the “shadow” areas that do not get the benefit of good air flow. These areas will be at a higher temperature than those directly in the air flow path. It is recommended that the unit is operated continuously under the worst case conditions for a period of 4 to 8 hours or until the inductor reaches thermal equilibrium. The true maximum temperature of the core can then be determined. Iron Powder core materials do have differing thermal conductivities which will effect their temperature gradient. Please refer to the Thermal Conductivity information.
Selecting a lower permeability core material will reduce the peak operating flux density and associated core loss. This reduction in core loss can be very significant and will, generally, more than offset any increase in winding losses.
The Micrometals Design Software is also available for a rapid solution to your requirements.
歡迎來到Bewise Inc.的世界,首先恭喜您來到這接受新的資訊讓產業更有競爭力,我們是提供專業刀具製造商,應對客戶高品質的刀具需求,我們可以協助客戶滿足您對產業的不同要求,我們有能力達到非常卓越的客戶需求品質,這是現有相關技術無法比擬的,我們成功的滿足了各行各業的要求,包括:精密HSS DIN切削刀具、協助客戶設計刀具流程、DIN or JIS 鎢鋼切削刀具設計、NAS986 NAS965 NAS897 NAS937orNAS907 航太切削刀具,NAS航太刀具設計、超高硬度的切削刀具、醫療配件刀具設計、複合式再研磨機、PCD地板專用企口鑽石組合刀具、粉末造粒成型機、主機版專用頂級電桿、PCD V-Cut刀、捨棄式圓鋸片組、粉末成型機、主機版專用頂級電感、’汽車業刀具設計、電子產業鑽石刀具、木工產業鑽石刀具、銑刀與切斷複合再研磨機、銑刀與鑽頭複合再研磨機、銑刀與螺絲攻複合再研磨機等等。我們的產品涵蓋了從民生刀具到工業級的刀具設計;從微細刀具到大型刀具;從小型生產到大型量產;全自動整合;我們的技術可提供您連續生產的效能,我們整體的服務及卓越的技術,恭迎您親自體驗!!
BW Bewise Inc. Willy Chen willy@tool-tool.com bw@tool-tool.com www.tool-tool.com skype:willy_chen_bw mobile:0937-618-190 Head &Administration Office No.13,Shiang Shang 2nd St., West Chiu Taichung,Taiwan 40356 http://www.tool-tool.com / FAX:+886 4 2471 4839 N.Branch 5F,No.460,Fu Shin North Rd.,Taipei,Taiwan S.Branch No.24,Sec.1,Chia Pu East Rd.,Taipao City,Chiayi Hsien,Taiwan
Welcome to BW tool world! We are an experienced tool maker specialized in cutting tools. We focus on what you need and endeavor to research the best cutter to satisfy users’ demand. Our customers involve wide range of industries, like mold & die, aerospace, electronic, machinery, etc. We are professional expert in cutting field. We would like to solve every problem from you. Please feel free to contact us, its our pleasure to serve for you. BW product including: cutting tool、aerospace tool .HSS DIN Cutting tool、Carbide end mills、Carbide cutting tool、NAS Cutting tool、NAS986 NAS965 NAS897 NAS937orNAS907 Cutting Tools,Carbide end mill、disc milling cutter,Aerospace cutting tool、hss drill’Фрезеры’Carbide drill、High speed steel、Compound Sharpener’Milling cutter、INDUCTORS FOR PCD’CVDD(Chemical Vapor Deposition Diamond )’PCBN (Polycrystalline Cubic Boron Nitride) ’Core drill、Tapered end mills、CVD Diamond Tools Inserts’PCD Edge-Beveling Cutter(Golden Finger’PCD V-Cutter’PCD Wood tools’PCD Cutting tools’PCD Circular Saw Blade’PVDD End Mills’diamond tool. INDUCTORS FOR PCD . POWDER FORMING MACHINE ‘Single Crystal Diamond ‘Metric end mills、Miniature end mills、Специальные режущие инструменты ‘Пустотелое сверло ‘Pilot reamer、Fraises’Fresas con mango’ PCD (Polycrystalline diamond) ‘Frese’POWDER FORMING MACHINE’Electronics cutter、Step drill、Metal cutting saw、Double margin drill、Gun barrel、Angle milling cutter、Carbide burrs、Carbide tipped cutter、Chamfering tool、IC card engraving cutter、Side cutter、Staple Cutter’PCD diamond cutter specialized in grooving floors’V-Cut PCD Circular Diamond Tipped Saw Blade with Indexable Insert’ PCD Diamond Tool’ Saw Blade with Indexable Insert’NAS tool、DIN or JIS tool、Special tool、Metal slitting saws、Shell end mills、Side and face milling cutters、Side chip clearance saws、Long end mills’end mill grinder’drill grinder’sharpener、Stub roughing end mills、Dovetail milling cutters、Carbide slot drills、Carbide torus cutters、Angel carbide end mills、Carbide torus cutters、Carbide ball-nosed slot drills、Mould cutter、Tool manufacturer.
Bewise Inc. www.tool-tool.com
ようこそBewise Inc.の世界へお越し下さいませ、先ず御目出度たいのは新たな
情報を受け取って頂き、もっと各産業に競争力プラス展開。
弊社は専門なエンド・ミルの製造メーカーで、客先に色んな分野のニーズ、
豊富なパリエーションを満足させ、特にハイテク品質要求にサポート致します。
弊社は各領域に供給できる内容は:
(1)精密HSSエンド・ミルのR&D
(2)Carbide Cutting tools設計
(3)鎢鋼エンド・ミル設計
(4)航空エンド・ミル設計
(5)超高硬度エンド・ミル
(6)ダイヤモンド・エンド・ミル
(7)医療用品エンド・ミル設計
(8)自動車部品&材料加工向けエンド・ミル設計
弊社の製品の供給調達機能は:
(1)生活産業~ハイテク工業までのエンド・ミル設計
(2)ミクロ・エンド・ミル~大型エンド・ミル供給
(3)小Lot生産~大量発注対応供給
(4)オートメーション整備調達
(5)スポット対応~流れ生産対応
弊社の全般供給体制及び技術自慢の総合専門製造メーカーに貴方のご体験を御待ちしております。
Bewise Inc. talaşlı imalat sanayinde en fazla kullanılan ve üç eksende (x,y,z) talaş kaldırabilen freze takımlarından olan Parmak Freze imalatçısıdır. Çok geniş ürün yelpazesine sahip olan firmanın başlıca ürünlerini Karbür Parmak Frezeler, Kalıpçı Frezeleri, Kaba Talaş Frezeleri, Konik Alın Frezeler, Köşe Radyüs Frezeler, İki Ağızlı Kısa ve Uzun Küresel Frezeler, İç Bükey Frezeler vb. şeklinde sıralayabiliriz.
BW специализируется в научных исследованиях и разработках, и снабжаем самым высокотехнологичным карбидовым материалом для поставки режущих / фрезеровочных инструментов для почвы, воздушного пространства и электронной индустрии. В нашу основную продукцию входит твердый карбид / быстрорежущая сталь, а также двигатели, микроэлектрические дрели, IC картонорезальные машины, фрезы для гравирования, режущие пилы, фрезеры-расширители, фрезеры-расширители с резцом, дрели, резаки форм для шлицевого вала / звездочки роликовой цепи, и специальные нано инструменты. Пожалуйста, посетите сайт www.tool-tool.com для получения большей информации.
BW is specialized in R&D and sourcing the most advanced carbide material with high-tech coating to supply cutting / milling tool for mould & die, aero space and electronic industry. Our main products include solid carbide / HSS end mills, micro electronic drill, IC card cutter, engraving cutter, shell end mills, cutting saw, reamer, thread reamer, leading drill, involute gear cutter for spur wheel, rack and worm milling cutter, thread milling cutter, form cutters for spline shaft/roller chain sprocket, and special tool, with nano grade. Please visit our web www.tool-tool.com for more info.